For the next installation in the “Meet the Team” series, we hear from Yuki Higa, a Process Engineer at Antheia. Read on to learn about Yuki’s fast-paced work in a downstream processing group.
What is downstream processing?
The high-level goal of downstream processing, or DSP, is to purify the broth produced by our fermentation tanks to create a usable product. The fermentation team will deliver the broth produced to the DSP group to essentially clean it up. There are impurities in the fermentation broth when it is first produced and our job is to remove as many of those as possible to get a clean and usable product at the end. A lot of the techniques we use in the lab take advantage of how the main molecule we’re aiming to isolate reacts in various environments.

Essentially, we’re the last group to touch the product before we ship it to the customer. Because of this, DSP is key for commercialization as our team provides the technical details and support required to produce large amounts of product at a manufacturing plant. During the manufacturing phase, if the product quality is not as expected, the DSP group can help troubleshoot and propose solutions to fix and prevent future problems.
Tell us about your background.
I did my undergrad at UC Berkeley, studying chemistry. I’ve always been interested in science, and was drawn toward chemistry – I enjoyed that it was a more controllable discipline. After college, many of my peers at UC Berkeley decided to pursue PhD programs in chemistry, but I was eager to enter the job force, so I pursued a chemical engineering master’s program at UC Irvine as a launch pad for a career.
After graduation, I started my professional career at Amyris doing similar work to what I’m doing today – namely conducting bench experiments and achieving pilot and manufacturing scale. I gained such valuable hands-on experience learning how to design experiments and analyze data, which has translated seamlessly to my work at Antheia.
I also met Suzy, my current manager, while at Amyris – she was a big reason I chose to come work at Antheia. She has been a great mentor to me and has helped me – along with many others – in our work in and outside of the lab. When you’re in the trenches, it can be hard to see the bigger picture, but one of Suzy’s strengths is making sure the pieces fit together so our work is successful and impactful.
What is your typical day like?
I work in process engineering, which is essentially the bridge between research and manufacturing. My team makes it possible to scale our work by creating processes at the bench scale and then using those parameters to inform our work at the pilot and manufacturing scale. As I focus on downstream processing, I’m most concerned about purification – my team takes the product from the fermentation team and purifies it, so that it meets all the customer specifications.
Most days, I split my time between benchwork and deskwork. The benchwork generally involves running experiments and analyzing the resulting data. It’s nuanced work since we do have to often make small adjustments, then run the experiments again. When we’re not doing benchwork, the team is generally doing literature research on various purification processes that have been used in the past to inform our own approach and inform the direction we take for our own purification pathway.
Lately, I’ve been researching new equipment to bring into the lab, as Antheia is in the process of expanding its downstream processes. I’ve been working to understand exactly what we need to replicate our protocols at the pilot and manufacturing scale, which gives us valuable data for future experiments. There is a lot of nuanced industry knowledge involved in this process, so having the opportunity to dig deep into this research will ultimately increase Antheia’s success rate when delivering final products and widen our competitive advantage.


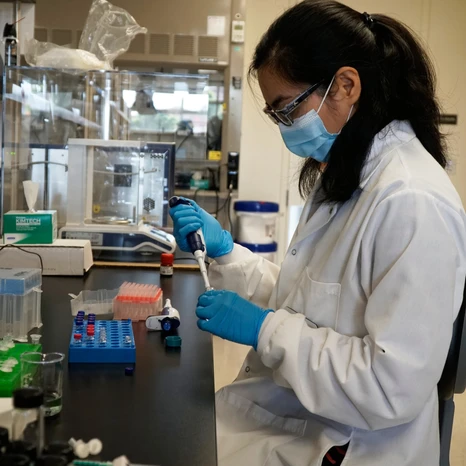
What’s your favorite part of your job, or the project you’re working on that you are most excited about?
I like to see my processes going to pilot or manufacturing. It’s validating to know that the data I’m gathering at the bench is strong enough to use at that scale, and it tells me that I’m designing experiments correctly and collecting usable data. Just this year, we went to a manufacturing facility to run a few experiments and they resembled what we saw at the pilot scale, which is always rewarding.
What’s the most unique part of your day-to-day?
The most unique part of being on the DSP team is the ability to see the full range of equipment and how your process translates across scales. We start off at a small scale in the lab, then see it translate to the pilot, and finally, at manufacturing scale. Many people, especially those that work at large companies, don’t get to see how their final product is made and aren’t familiar with the in-depth process and logistics behind it. Working at Antheia gives me the unique opportunity of being able to track a project along its lifespan.
What is your high-level impact at the company?
I see a direct connection between my work in the lab and the final product being delivered to our manufacturing partner. We went to pilot at the beginning of the year and created a proof of concept product that was shared with the customer and implemented into their process for evaluation. This is a clear demonstration of my team’s impact – helping a partner take an idea from conceptualization to commercialization.
What are you looking forward to most in Antheia’s future?
I’m most looking forward to going to manufacturing to see this process all the way through. I really believe in Antheia’s mission and our platform for transforming the supply chain for plant-based medicines – seeing how close we are to manufacturing scale is a significant milestone and I’m excited to reach it with this team.
Interested in learning more about our team? Read more about our Scientist (Ken) and RA (Cat).
*Photo credits: Daniel Yim